Ultimate Guide to Cleaning Electronics
In the process of assembling, reworking or repairing printed circuit boards (PCB) for electronic devices, the discussion inevitably turns to whether or not to clean the PCB. Cleaning adds time and expense to the process, and doing it wrong can cause more harm than good. This guide will walk you through the reasons to clean PCBs, and the best practices for electronics cleaning.
Index of topics
- Why Clean a Printed Circuit Board (PCB)?
- What Is Ionic Contamination?
- What Are The Most Common Ionic Contaminants From The Bare Board Fabrication?
- What is White Residue on an Electronic Circuit Board?
- How Do You Perform Ionic Contamination Testing?
- How Do You Remove White Residue From an Electronic Circuit Board?
- What are the Different Methods of Cleaning Electronic Circuit Boards?
- Does the Flux Type Affect the Effectiveness of the PCB Cleaning Process?
- What Factors Cause Difficulty Cleaning Flux Residues from PCBs?
- How do you clean a PCB after soldering?
- How Do I Use the Straw Attachment On The Aerosol Flux Remover to Improve Cleaning Effectiveness?
- How Do I Clean Under Components With An Aerosol Flux Remover?
- Does the Angle of The Spray Affect Cleaning Effectiveness When Using an Aerosol Flux Remover?
- Are There Right and Wrong Ways To Use Cleaning Tools Like Brushes, Swabs and Wipes?
- When Is a Final Rinse Required When Cleaning a PCB?
- What is the most popular electronic cleaner?
Why Clean a Printed Circuit Board (PCB)?
Since cleaning PCB’s is not always required and adds time and cost to the production or repair process, some justification may be required.
Improve Aesthetic Appearance of PCB
If you are a contract manufacturer of PCB’s, the visual appearance of the board reflects on your work. A clear, greasy-looking residue around a solder joint may raise flags for your customer’s incoming QC inspectors. If the flux residue chars and forms spots on the solder joints, it may look like a true defect like a solder joint void or “blow hole”. If the flux residue is from a rework process, it acts as a fault tag in the rework area, calling attention to the work even if there shouldn’t be a concern.
Improve Reliability of PCB
Reliability requirements are generally driven by the nature of the final product. For a disposable product like a computer keyboard, nobody loses their life if it stops working. In that case, an EMS supplier may use no-clean flux and forgo the cleaning process. On the other end of the scale, requirements for pacemaker electronics, where board failure could directly lead to death, are going to be much stricter. In that example, cleaning will be required after assembly and any subsequent rework, and the process will be thoroughly tested for effectiveness and repeatability. Long-life durable goods may fall somewhere in-between, with cleaning a requirement, but without the rigid testing and controls.
Prevent Corrosion on Components and PCB
Flux residues left on electronic circuit boards are acidic. If they aren’t removed with a cleaning process, the residues can draw in ambient moisture from the air and lead to corrosion of component leads, and PCB contacts.
Corrosion on failed assembly in QFP area (photo courtesy of Foresite)
Avoid Adhesion Problems with Conformal Coating
Most people understand that when painting something, the surface must be prepared so it is absolutely clean. Otherwise, the paint will quickly lift off the surface and peel off. The same logic applies to conformal coating, even when the contamination is from no-clean flux. “No-clean” refers to the amount of ionic material left after soldering. It has nothing to do with whether or not coating can stick to it.
When there are flux residues left on the PCB before the coating process, it is common to see the coating lift or delaminate from the surface of the board. This is evident when the pockets are isolated around solder joints rather than the overall surface (the exception being the bottom of a wave soldered PCB).
To make matters worse, coatings are generally semi-permeable, so breathe to a certain extent. Moisture can enter and soak into the flux residue, and potentially lead to corrosion.
Flux residues causing coating uplift (photo courtesy of NPL)
Prevent Dendritic Growth from Ionic Contamination
Polar or Ionic particles left from flux residue and other sources, when exposed to moisture from the ambient air and when current is applied, can link into a chain or branch called a dendrite (fig 1). These dendrites are conductive, so form an unintended trace that cause current leakage or, over a longer period of time, even a short circuit.
Fig 1 – dendrite formation
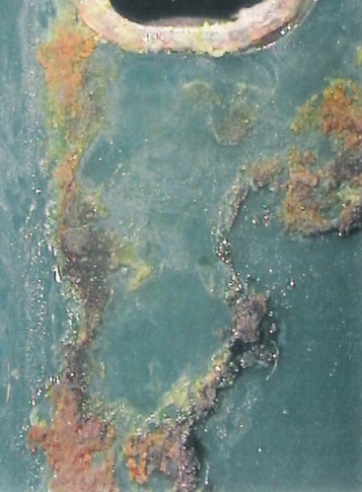
Dendritic grown between solder pads, caused by ionic contamination (photos courtesy of Foresite)
What Is Ionic Contamination?
What is Polar Contamination?
Ionic contaminants are remains of flux that are left behind during the assembly process. Ionic compounds are held together by electrostatic forces and the compound itself has a zero net charge. These materials will disassociate when exposed to water. These are composed of positively charged cations and negatively charged anions. A simple example is table salt (sodium chloride), composed of a single positive sodium cation which lacks one electron, and a negatively charged chloride anion (Cl), which has an extra electron. Polar compounds on the other hand can have a positive charge on one side of the molecule and a negative charge on the other side of molecule; these molecules never split apart. Water, Isopropanol (or IPA) is an examples of a polar molecule.
When populating the board with components, the components themselves also can carry various ionic/conductive contaminants to your assembly including cutting oils/fluids, biocides, and corrosion preventatives. Be aware of common nonionic materials that can also affect the assembly steps – process oils, mold releases, etc. can be detrimental down the line.
What Are The Most Common Ionic Contaminants From The Bare Board Fabrication?
Common Moisture Trapped in the “Layering” Process
Water is a polar contaminant. It is conducive for dissociating other ionic materials which lays the foundation for conductive mishaps (dendritic growth, ECM, etc). It is common practice to “bake” the boards to remove extraneous moisture.
Corrosion from PCB fabrication contamination (photo courtesy of Foresite)
Etching Chemicals
These are highly conductive and can be corrosive as well. They must be chemically neutralized and removed/rinsed and are well-known as sources for current leakage.
Flux Residues from Soldering
Heavy no-clean flux residue with visible copper corrosion (photo courtesy of Foresite)
Everyone is familiar with flux residues. Fluxes, whether in liquid, cored wire, or compounded as a paste, can leave residues that can cause serious reliability defects if not removed. Common conductive flux residues from the soldering process can include various unreacted activators, binders, rheology components, and saponifiers. Among these are numerous iterations of acids (abietic, adipic, succinic among others), highly basic ingredients (amino compounds), and even constituents found in “soaps” such as phosphate and sulfate ions. All of these must be cleaned from the substrate, whether by strict solvent cleaning such as vapor degreasing or by aqueous chemistries in the common batch or inline cleaners seen on the manufacturing floor.
Inter-Layer Residues from Drilling and Via Plating Processes
Dendritic grown between solder pads, caused by ionic contamination (photo courtesy of Foresite)
In addition to these widely seen residues, residues from the cleaning process chemistry itself must also be removed. This is noticed more in the aqueous cleaning systems. Many use saponifiers to neutralize and emulsify the flux residues and make them easier to rinse/remove from the substrate. These components themselves are highly polar and ionic and can also enhance the dendrite and/or ECM mechanism if not removed. In addition, corrosion preventatives and surfactants are commonly employed in these products. This is not a bad thing in itself, but care must be taken to ensure they are removed along with the soils during the cleaning process.
How Do You Perform Ionic Contamination Testing?
Poor quality control from PCB fabrication, to the soldering and component population, to the final cleaning stages, are all potential sources of contamination. Many of these can be found by ionic contamination testing and analysis such as ROSE testing, ion extraction, and chromatography, as well during initial high humidity validation testing at the beginning of the project.
Strict quality control and standard operating procedures during the PCB assembly and the stages of assembly manufacturing and validation testing can go a long way in preventing a reliability nightmare. Just think – simple mishandling of a part by an operator not using gloves can transfer salts and oils from skin to the substrate that could potentially be catastrophic for your item!
What is White Residue on an Electronic Circuit Board?
White residue is generally a symptom of ineffective PCB cleaning. Common conductive flux residues from the soldering process can include various unreacted activators, binders, rheology components, and saponifiers. Among these are numerous iterations of acids (abietic, adipic, succinic among others), highly basic ingredients (amino compounds), and even constituents found in “soaps” such as phosphate and sulfate ions. When a cleaner does not fully dissolve all the constituents, or the cleaner is not allowed to flow off the PCB, the remaining solvent can evaporate off and leave behind residue that is either white or like water spots.
White flux residue with visible copper corrosion (photo courtesy of Foresite)
How Do You Remove White Residue From an Electronic Circuit Board?
White residues can generally be cleaned by a flux remover. If the residues are the result of insufficient solvency of the original cleaning process, a stronger solvent cleaner may be required. Often agitation is required to remove the residues, which may include a wipe, swab, brush, or an aerosol with a brush attachment. Follow these steps to remove white residue:
- Spray the residue with a strong solvent.
- While the area is still wet, scrub with a clean tool like a wipe, swab, or brush.
- Spray the cleaned area and surrounding areas with the same solvent, angling the board so the rinse is able to run off.
Flux-Off® Rosin with a brush attachment
What are the Different Methods of Cleaning Electronic Circuit Boards?
PCB flux removal can either happen at the benchtop, which generally requires a manual cleaning method. This is common for low volume electronic PCB assembly, rework, and repair. Manual cleaning methods are generally more laborious and less repeatable, so results may vary from operator to operator. For higher volume assembly or reduced variability, more automated cleaning methods are used.
Manual Flux Removal Methods
- Aerosol– Aerosol flux removers have the advantage of a sealed system, which ensures fresh solvent every time, and agitation provided by the spray pressure and pattern. A straw attachment is generally included to spray into areas with greater precision.
- Aerosol w/brush attachment– A brush can be added to the aerosol nozzle, so the solvent sprays through the brush as you scrub.
- Trigger spray– Trigger spray bottles are more common for water-based cleaners and isopropyl alcohol (IPA), but not for aggressive solvent cleaners.
- Liquid immersion– The PCB can be immersed into a tray or bucket of solvent cleaner, with cleaning tools like swabs and brushes used as needed for tenacious soils. Cleaning performance can be further improved by heating the solvent, but this should only be done with nonflammable flux removers.
- Spot cleaning with a swab– A cotton or foam swab can be saturated with a mild solvent like isopropyl alcohol, often from a pump dispenser or “dauber”.
- Presaturated wipes and swabs– For added convenience, wipes and swabs are available presaturated with a mild solvent like isopropyl alcohol.
Automated or Semi-Automated Flux Removal Methods
- Ultrasonic– Ultrasonic cleaning equipment use sound waves to create implosions within the flux residue, breaking it apart and lifting it off the PCB. Most equipment have the option of heating the solvent to increase cleaning performance. Only use this option with a nonflammable flux remover. Cross contamination can be a concern, so change solvent regularly. Ultrasonic cleaning might be too rough on sensitive components like ceramic-based resisters.
- Vapor degreaser– Vapor degreasing is the go-to process for the highest precision cleaning, like used for aerospace and medical electronics. PCBs can be submerged in a sump of boiling solvent, in a rinse sump with ultrasonics, and rinsed in solvent vapors. Special solvents need to be used that are azeotropes or near-azeotropes, so will not change as the solvents are boiled off and reconstituted in a continuous cycle.
- Batch flux remover– Basically a dishwasher for electronic circuit boards. PCBs are stationary in a rack, and the flux remover (usually water-based) is sprayed over the assembly. The PCB stays in place as the machine goes through the wash, rinse and finally dry cycle.
- Inline flux remover– An inline washer is more like a carwash for electronic circuit boards. PCBs travel on a conveyor through wash, rinse and dry zones. Water-based flux removers are used.
Does the Flux Type Affect the Effectiveness of the PCB Cleaning Process?
The type of flux can have a big impact on the cleaning process. R, RA and RMA fluxes are generally easier to remove with standard flux removers and isopropyl alcohol. No-clean fluxes are intended to stay on the PCB, so can be more difficult to remove. They may require more a more aggressive solvent flux remover, addition agitation like brushing, or a heated solvent. Aqueous fluxes are generally designed to be removed in a batch or inline cleaning system with straight deionized water or water with a saponifier. Alcohol-based or specially formulated solvents can also be used to clean aqueous fluxes, but the same cleaners may have mixed results on other types of fluxes.
The short answer is to match the flux remover with the flux type. This can be challenging for an EMS supplier that may have to use a variety of fluxes as required by their various customers. Flux removers are available that can break down a large variety of fluxes, and changing variable like cleaning time, agitation, and additional heat can make up the difference.
For water-based cleaners run in a batch or inline cleaning system, cleaner concentration can be adjusted, cycle time increased, and temperature increased to improve performance.
What Factors Cause Difficulty Cleaning Flux Residues from PCBs?
Any process engineer will tell you that the key to designing a repeatable process is to control the variables. When removing flux from electronic circuit boards, there are a number of variable that can drastically change the cleaning performance of a cleaner and process:
- Flux type – The type of flux can have a big impact on the cleaning process. R, RA and RMA fluxes are generally easier to remove with standard flux removers and isopropyl alcohol. No-clean fluxes are intended to stay on the PCB, so can be more difficult to remove. They may require a more aggressive solvent flux remover, additional agitation like brushing, or a heated solvent. Aqueous fluxes are generally designed to be removed in a batch or inline cleaning system with straight deionized water or water with a saponifier. Alcohol-based or specially formulated solvents can also be used to clean aqueous fluxes, but the same cleaners may have mixed results on other types of fluxes.
- Higher solids flux – Cleaning a PCB made with a mix of soldering technologies can be a particular challenge. Tacky fluxes or other types with a high level of solids can be more challenging to clean, require more cleaning time, soak time, or additional agitation.
- Amount of flux – A thicker layer of flux residue is more soil to remove, and can create flux dams under low stand-off components. This prevents flux remover from fully penetrating under the component.
- Soldering temperature – Higher temperatures have a greater tendency to bake-on flux residues, making them more difficult to remove. High temperature soldering may require more cleaning time, soak time, or additional agitation.
- Lead-free solder> – Lead-free soldering generally requires higher soldering temperature and more highly activated fluxes. Flux residues left from a lead-free soldering process may require more cleaning time, soak time, or additional agitation, and you may actually have to consider a more aggressive flux remover that is engineered for lead-free processes.
- Time between soldering and cleaning process – It is not unusual to finish the assembly on Friday, come back on Monday to clean and be surprised with white flux residues. As flux residues sit on the PCB, volatiles continue to flash off and it becomes more difficult to remove.
If you are suddenly surprised by white residues or some other clear evidence of a cleaning problem that didn’t exist before, step back and look at your process before calling for help. Has anything changed? That will be the first question a technician will ask, and necessary to know before you can identify and solve the problem.
How do you clean a PCB after soldering?
How do you remove solder flux?
The most common way to clean flux residues from a repair area is to saturate a cotton or foam swab with isopropyl alcohol or another cleaning solvent, and rub it around the repair area. While this may be adequate for no-clean flux, where the goal is a visually clean PCB, this may not be clean enough when more heavily activated fluxes are involved, like RA or aqueous. The dirty little secret is that flux residues will not evaporate along with the solvent. You may dissolve the flux, and some of the residues will soak into the swab, but most of the residues will settle back onto the board surface. Many times these white residues are more difficult to remove than the original flux.
Flux residues don't evaporate along with the solvent.
One quick and easy improvement to this process is to rinse the board after swabbing around the repair area. While the solvent is still wet, spray over the entire board with an aerosol flux cleaner. Hold the PCB at an angle to allow the solvent to flow over the board and run off, along with any residues that are picked up.
The straw attachment that comes with aerosol flux removers is a good way to increase the spray force and penetrate under the components.
Aerosol with straw good for cleaning under components
Chemtronics offers the BrushClean™ system with many of their flux removers. The cleaning solvent sprays through the brush, so agitation can be increased by scrubbing while spraying. To absorb the flux residues, a lint-free poly-cellulose wiper can be placed over the repair area, and the spraying and scrubbing can occur over the material. Then remove the wipe and brush attachment, and spray over the board for the final rinse.
Aerosol brush attachment over a wiper dissolves and absorbs flux residues at the same time.
How Do I Use the Straw Attachment On The Aerosol Flux Remover to Improve Cleaning Effectiveness?
The use of the straw attachment allowed for a more controlled spray, thus eliminating excessive solvent waste. The straw was also useful in directing exactly where the solvent went. This allowed the user to guide the solvent under the component. Without the straw attachment, the solvent was sprayed at the target area (for instance, the sides of the component); however, much of the material was wasted on areas surrounding the target and very little ended up traveling under the component (see Figure 1).
Figure 1: Visual comparison of an aerosol spray without (left) and with a straw attachment.
How Do I Clean Under Components With An Aerosol Flux Remover?
Best results were obtained when both corners and sides of each contaminated component were addressed, as opposed to focusing on only one or the other, corners or sides. Directing solvent directly into the corners helped to break up any flux dams located there. Because the corners were cleared first when the sides of the components were addressed, the number of channels opened to allow the solvent to pass was greater than it was when corners were not addressed first. The more open channels available, the greater the opportunity for the flux to be exposed to the solvent, and as a result, the higher likelihood that all flux trapped under the component will be able to flow out from under the component.
The choice to use an oscillating or stationary spray was dependent on the size of the component. For a small component it was sufficient to use a stationary spray on the component sides; however, for larger components, a cleaner board was achieved when the spray oscillated back and forth across each side of the component. This oscillating spray gave the solvent the opportunity to flow up, under the component from many angles, similar to the way that the flux had.
Does the Angle of The Spray Affect Cleaning Effectiveness When Using an Aerosol Flux Remover?
In our testing, an exact straw angle of 30o, 45o, or 60o to the board had no impact on the cleanliness of the board. General downward or upward angles were sufficient. In order to make the most of the straw, think about the direction in which the residues need to travel. When trying to remove residues from under a component, spray close to the board at an angle that guides the solvent under the component. When all of the residues have been removed from underneath the component, spray from on top of the component, angling out along the edges to push any residues out, away from the component.
Are There Right and Wrong Ways To Use Cleaning Tools Like Brushes, Swabs and Wipes?
Handheld brushes and swabs left the board looking dirtier than it started. Brushes and swabs spread partially solvated flux around the components which then dried, leaving a white residue. None of the polyurethane foam swabs held-up well in this application. Foam swabs became flimsy when saturated with aggressive solvents and were easily torn. Another problem with handheld tools was that the solvent evaporated too quickly. Best results were achieved when a final rinse was utilized (see Figure 2). The key is not to let the board dry out. When the board dries, the partially solvated flux dries leaving the white residue mentioned earlier. A slower evaporating solvent, like IPA, would avoid the evaporation issue but should be followed by a rinse (see more details on rinsing below). In addition, some solvent may travel under the component during scrubbing, but without the force of an aerosol spray, the likelihood that the residues under the component will be pushed out is slim.
Figure 2: Board cleaned with a handheld brush. The components were wetted, and then the brush was wetted and used to scrub the contaminated area. The board in the first picture did not undergo a final rinse. The board in the second picture did (Note: all flux was not removed).
Some solvent cleaners come with a brush that attaches directly to the spray head, and the solvent flows through the brush at a slow rate (see Figure 3). This is particularly common in defluxers available in Europe. Brush attachments produced results that were a step above handheld tools, due to the benefit of a constant supply of virgin solvent. However, they did not produce the same level of cleanliness observed in aerosol only cleaning. The brush attachment allowed for scrubbing problem areas, which can be beneficial. However, the force of an aerosol through a straw attachment produced similar results.
Brush attachments, like handheld tools, have the potential to introduce new contaminants. In addition, for a brush attachment to reach its full potential, a separate aerosol is required for cleaning under components and for the final rinse. Like handheld tools, without the force of an aerosol spray, some solvent may travel under the component during scrubbing; however, the likelihood that the residues under the component will be pushed out is slim. Because the use of a brush attachment requires that the target area remain saturated, the target area remains in a solvent pool throughout the cleaning period. This increases the likelihood that residues may only be relocated on the board instead of being removed completely. A final rinse, then, was found to be especially important, to ensure that all of the residues were removed from the board (see Figures 4 and 5).
There is a commercially available brush system that provides a separate brush mechanism for cleaning, which is continually fed by the aerosol can. No cleaning advantages to this system were observed compared to a brush attachment. A brush system or attachment is often used to reduce solvent usage, but this advantage is greatly decreased if a proper rinse is applied.
Figure 3: Brush attachment
Figure 4: Board cleaned with brush attachment (no separate aerosol was used). No pre-rinse or final rinse utilized. White residue shown around QFN B and QFP, respectively.
Figure 5: Board cleaned with brush attachment (separate aerosol was used for pre-rinse and final rinse). Some white residue shown around QFN B and QFP, respectively.
When Is a Final Rinse Required When Cleaning a PCB?
In our testing, the final rinse was found to be a necessary step. This step ensures that all of the solvated flux residues, which have been removed from under and around components, flow off the board completely, and are not simply relocated.
At first, glance, what we recommend may seem over-the-top. Why go through all the trouble and expense of thoroughly cleaning under the components when no one can see the difference? It all comes down to the reliability requirements of the electronics. For disposable electronic devices assembled with no-clean flux, an overall rinse may be all that is needed for acceptable results. If higher reliability is required, greater care is needed, with the techniques noted above, to prevent latent failure of the final device from ionic contamination. Spending the time and effort up-front is often money well spent.
What is the most popular electronic cleaner?
Chemicals are found throughout the electronic assembly and repair process, but no solvent is more common than isopropyl alcohol. It is universally used for cleaning and as a main constituent of fluxes, but how much do you really know about isopropyl alcohol?
Isopropyl alcohol (CAS #67-63-0) is also referred to as IPA, isopropanol, 2-propanol, and even rubbing alcohol. It dissolves a wide range of polar and non-polar soils, is it is often used to dissolve and remove light oils, fingerprints, cutting fluids, flux residues, carbon deposits, and mold release. It is also readily miscible in water, so can be used as a drying agent as well.
For electronic printed circuit board (PCB) assembly, you will find isopropyl alcohol being used to clean flux residues from recently soldered circuit boards or in PCB repair and rework. IPA is also used to remove solder paste or adhesive from SMT stencils. Maintenance cleaning with isopropyl alcohol is common for removing caked-on and burnt-on flux from SMT reflow ovens, wave soldering fingers, selective soldering nozzles, pallets, and anywhere else flux tends to collect in automated soldering processes.
Many other flux removers are available to clean specific fluxes, a broader mix of fluxes, and for specific cleaning processes. Contact Chemtronics for more information on how we can improve your PCB cleaning operation: chemtronics@itw-cc.com or +31 088 130 7400.