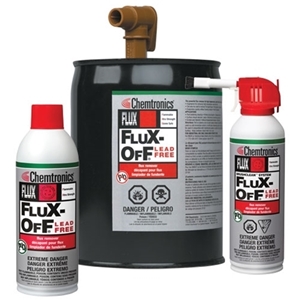
TDS
SDS (GHS)
Flux-Off® Lead-Free Flux Remover
Flux-Off® Lead-Free Flux Remover is an extra strength solvent that removes heavy and encrusted flux deposits resulting from high temperature lead-free soldering applications. This powerful cleaner quickly removes all types of flux, oxide particles, dust, grease and oil, and then evaporates quickly leaving no residues.
Available with The BrushClean™ System - Gentle scrubbing action of a brush combined with high performance flux remover. Click here for more information.
Features & Benefits
- Engineered for removing high temperature, lead free flux
- Can also be used to remove Tin/Lead fluxes
- Evaporates quickly without leaving residue
- All-Way Spray valve - even sprays upside down
- Flammable
- RoHS Compliant
- Available with BrushClean™ System
Applications
- Formulated specifically for lead-free flux removal
- Ideal for removing heat-degraded flux
Shelf Life | 5 yrs. |
---|---|
Shipping Name | Consumer Commodity ORM-D |