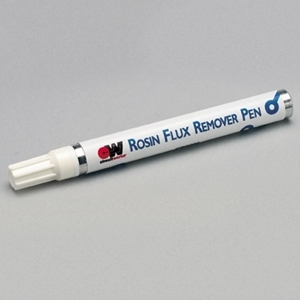
TDS
SDS (GHS)
CircuitWorks Flux Remover Pens
CircuitWorks® Flux Remover Pens are designed specifically to remove each type of flux:
- Rosin Flux Remover Pen quickly cleans type R, RMA, and RA flux residues.
- No Clean Flux Remover Pen precisely removes both organic and synthetic low solid no clean fluxes.
- Lead-Free Flux Remover Pen quickly cleans type R, RMA, and RA rosin flux residues as well as organic and synthetic no clean fluxes used in higher heat lead-free applications.
Features & Benefits
- Completely removes flux in seconds
- Spot cleans tight tolerance areas on circuit boards
- Marker dispenser provides controlled spot cleaning
- Dries fast
TYPICAL APPLICATIONS
CircuitWorks Flux Remover pens remove flux residues and clean precise areas on:
- Printed Circuit Boards
- Chip Carriers
- Heat Sinks
- Surface Mount Device Pads
- Switches
- Sockets
Shelf Life | 5 yrs. |
---|---|
Shipping Name | Consumer Commodity ORM-D |
Specs | ANSI/IPC J STD-001, IPC-7711 |