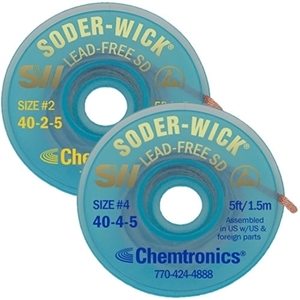
TDS
SDS (GHS)
Soder-Wick Lead-Free Desoldering Wick
Soder-Wick® Lead-Free desoldering wick is the state of the art in desoldering technology. It is specially designed for removal of today’s high-temperature lead-free solders. The single layer weave used for Soder-Wick® Lead-Free desoldering wick is lighter in mass than any other desoldering wick available and allows for lead-free solder removal at lower temperatures. Soder-Wick® Lead-Free desoldering wick responds faster than any other conventional desoldering braid. This unique design minimizes overheating and requires less “contact” time thus preventing heat damage to the PCB and sensitive components. For Lead-Free rework, Soder-Wick® has the answer.
All wick is sealed in nitrogen-purged packaging to avoid corrosion and loss of performance from moisture and oxygen.
Related Content: Desoldering Braid Tips & Tricks
Features & Benefits
- Engineered specifically for high temperature, lead-free solders
- Transfers heat to the solder joint more quickly and efficiently than conventional desoldering braids
- Specifically designed for all lead-free solders
- Can also be used with Tin/Lead solders
- Soder-Wick® Lead-Free packaged in ESD-safe static dissipative bobbins
- Minimizes the risk of damage associated with static electricity
- Non-corrosive ultra high purity no-clean flux
- Will not leave ionic contamination on the boards
- Especially effective at removing residual solder from SMT pads
- RoHS Compliant
- Patent Pending
Applications
- Soder-Wick® Lead Free safely removes solder from all lead free applications
Specifications:
- MIL-F-14256 F
- NASA-STD-8739.3 Soldered Electrical Connections
- DOD-STD-883E, Method 2022
- ANSI/IPC J STD-004, Type ROL0
Specifications |
ANSI/IPC J STD-004 Type ROL0 |
---|---|
Shelf Life | 2 Yrs |
Shipping Name | Copper Wire |