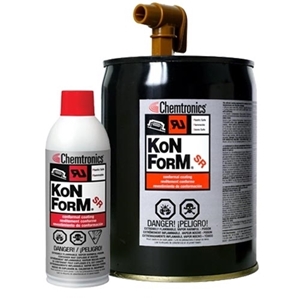
TDS
SDS (GHS)
Konform® SR Silicone Conformal Coating
Konform® SR provides maximum flexibility for extreme temperatures. This transparent conformal coating offers ideal protection for both rigid and flexible printed circuit boards. Cured coatings are hydrolytically stable, and retain their physical, electrical properties after high temperature and humidity exposure. Konform® SR will not stress delicate circuit components.
Konform SR is available in three different viscosities to match your application process:
- Standard viscosity - 40± 5 cps
- Medium viscosity - 60± 5 cps
- High viscosity - 120± 5 cps
CLICK HERE FOR CONFORMAL COATING SELECTION GUIDE
FEATURES & BENEFITS
- Engineered for applications where flexibility and high-temperature resistance are required
- Silicone coating stable from -85°F/-64°C to 390°F/199°C
- High dielectric strength of 1100 volts/mil
- Easily removed with Electro-Wash® Two-Step or CircuitWorks® Conformal Coating Remover Pen
- Meets MIL-I-46058C, Type SR
- Compliant to IPC-CC-830A
- RoHS Compliant
- UL Recognized, File E76307
- UL 94 V-0
- Contains a UV indicator for Quality Control inspection using medium intensity light at 265-335 nm
APPLICATIONS
- Extends component life by protecting against adverse environments
- Perfect insulation properties, excellent flexibility
- Resists moisture, salt, fungus, corrosive vapors, and severe environments
- Engineered to withstand the heat generated by electronic circuitry as well as climatic temperatures
Specifications | MIL-I-46058C Type SR, IPC-CC-830A,UL Recognized |
---|---|
NSN | 5970-01-417-4152 |
Shelf Life | 1 yr |
Shipping Name | Coating Solution |